HR for Lean & Lean for HR
Most organizations and HR professionals in a Lean Journey do not fully understand the role of HR in Lean and how to leverage that role to more effectively transform and continually improve their organization.
Main Benefit:
This course will focus on how HR teams can not only effectively partner with their business operations team but also how to strategically lead the organization while developing and engaging its people in continuous improvement.
Who should attend? This workshop is directed to the HR and members of the Lean Leadership and/or Operations Team
Duration: 2 days Limited to: 26 Participants
Instructor
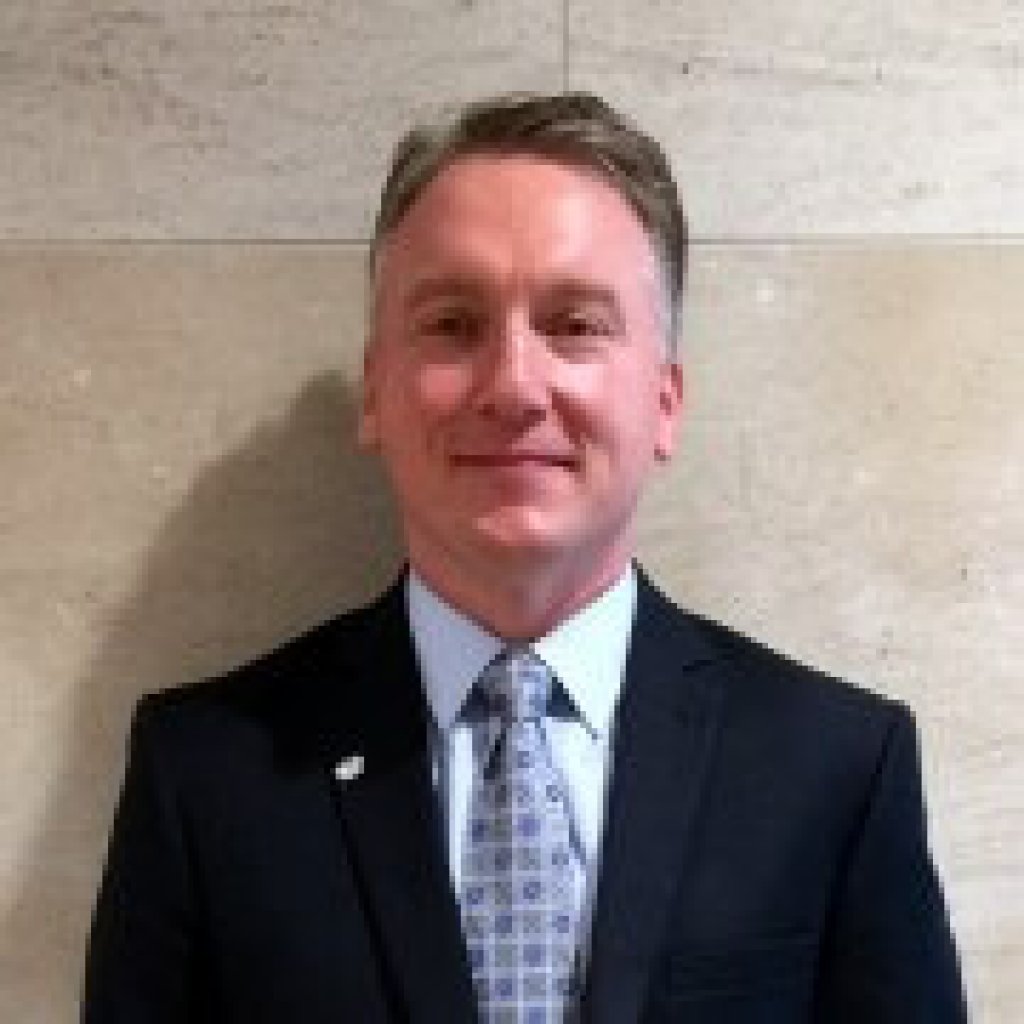
Darril Willburn – 20 years experience on Lean Management
Darril has led the development and implementation of some of the most important leadership development programs across Toyota Motor Manufacturing North America. He also led the implementation of the Toyota Way 2001 at Toyota’s largest manufacturing plant in North America and worked with The Toyota Institute in Japan to develop the Toyota Business Practice (TBP). While at Toyota, he studied the Toyota Production System as a student of OMDD, Toyota’s internal Sensei group.
He was also part of the team that launched Toyota Motor Manufacturing Texas, where he led the assimilation and training of new to Toyota management.
In the last 10 years he has work with clients like, Wrigley Europe, M&M Mars, Valero Energy, Kimberly-Clark, Monomoy Capital Partners, and Toyota Motor Manufacturing. Darril is also an active speaker delivering presentations and keynote speeches on Lean Principles around the globe including:
- Harvard Business Review-Latin America, lecture series in Chili, Equator, Mexico
- Lean Conference in Brazil
- MM Mars Latin American Leadership Team Retreat
- Abu Dhabi Talent Conference
- Washington State Government Lean Seminar
- Lithuanian Prime Ministers Conference
- Minister of Defense-Lithuania
- ISM University of Management and Economics, Vilnius, Lithuania
- Monomoy Capital Partners Annual CEO meeting
Darril is passionate about sharing the principles, culture and practices of Lean Leadership and Management
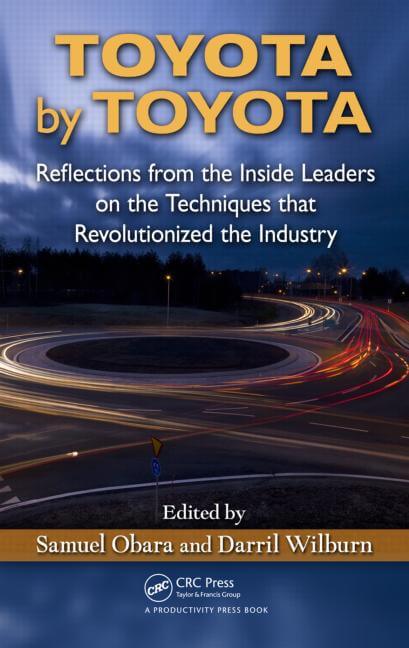
Darril is co-author of Toyota by Toyota
TRAINING AGENDA: BODY OF KNOWLEDGE
- Foundational Lean Principles
- Continuous Improvement and Respect
- Sub components of Courage, Humility and Kaizen
- Leaders that model and teach the balance of courage and humility can build a culture of continuous improvement that shows the highest level of respect for people. Once organizations align their actions with these principles then excellence is the natural outcome.
- Leading the establishment, communication and continuous improvement of the purpose or mission of the organization
- Facilitating not only the development of the values but also the “Plan Do Check Act”
- HR’s role in making “Job Security and No Layoffs” not only a priority but also a reality
- Establishing clear roles and responsibilities for the all the members of the organization as well as the departments/functions of the organization
- “Job Analysis” and determining the “Lean Competencies” for each Role
- Role in convincing and engaging top leadership in the Hoshin Kanri or Strategy Deployment process in order to align top to bottom and across the organization
- Utilizing Behavior Based Assessments for hiring and promotions
- Behavior Based” Interviewing Process
- Implementing an effective On-Boarding Process for all levels
- How to training and develop a lean workforce to engage in standardization and problem solving at all levels and functions in the organization
- Designing and implementing policies and practices to support lean
- Motivate and manage knowledge workers and bring out the best in people
- How to design in “checks and balances” for management accountability
- How to develop visual control for “team member accountability”
- How to connect performance management and compensation to the “Lean Daily Management Development System”
- Designing and implementing effective & partnering Safety strategies
- Conflict Management and Corrective Action systems based on problem solving instead of discipline or punishment
- HR processes mapping, waste elimination and standardization
- HR “Call Center” for problem solving and efficiency
- Communication Systems and Standards
- Implementing Family & Community Involvement Activities
- Utilizing Organizational Satisfaction Surveys for building Trust and Continuous Improvement
- Self assessment for your organization to grasp its Lean Management System and Role of HR “current state”
- Identify gaps or problems exisitng in your organization
- Prioritize the gaps identified
- Begin action planning to address the gaps
- Utilize Inventory Assessment tool to guide discussion and problem solving back at your organization.
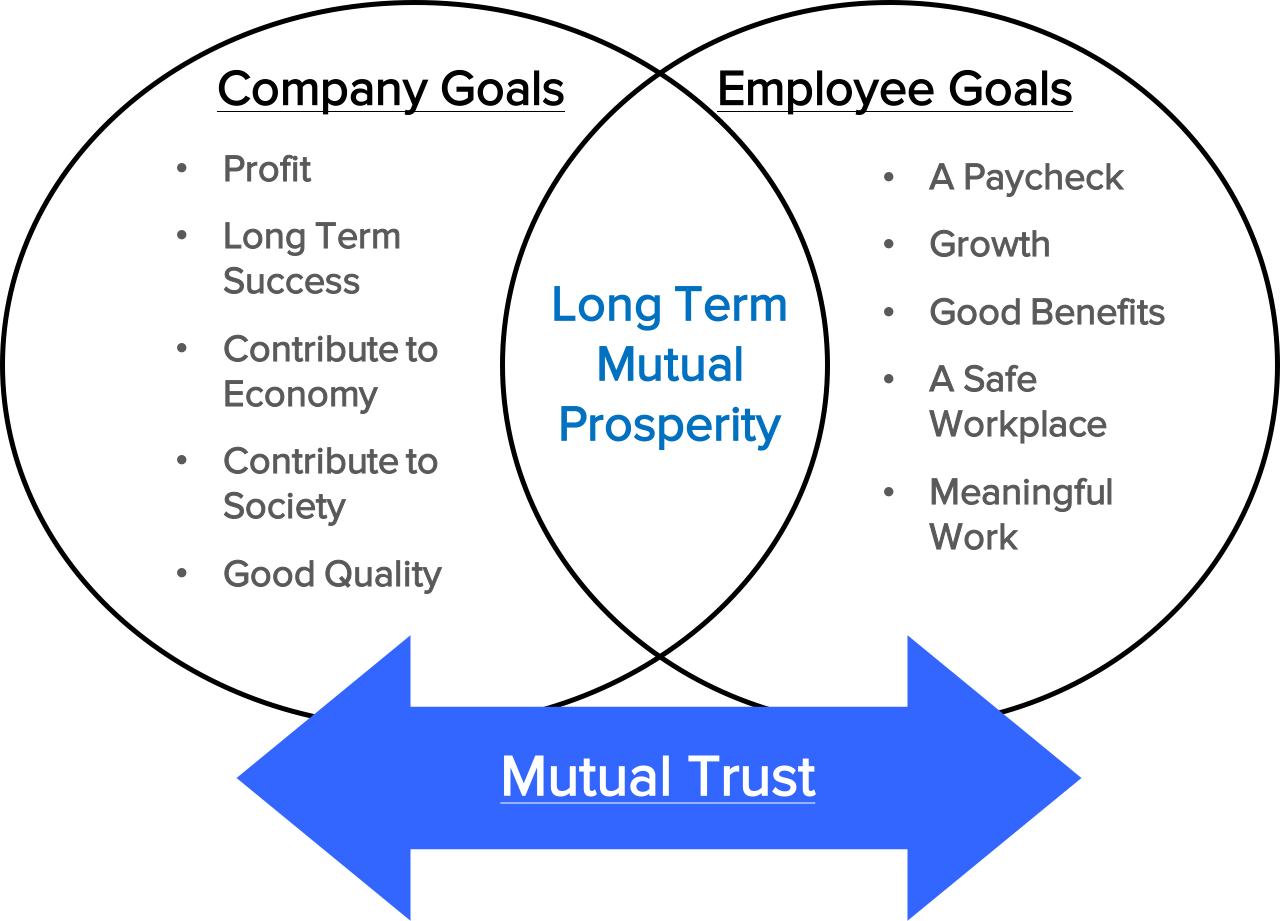