Lean Manufacturing Simulation
100% Practical Learning of Lean principles
Our practical learning system aims to involve participants in a real scenario where they can experience the traditional work systems, living day to day problems, about lead time, quality, customer & employees satisfaction, inventory among others,
Participants will DISCOVER by doing the benefits of the lean principles applied to the operations, delivering performance improvements in quality, delivery, inventory, among other indicators,
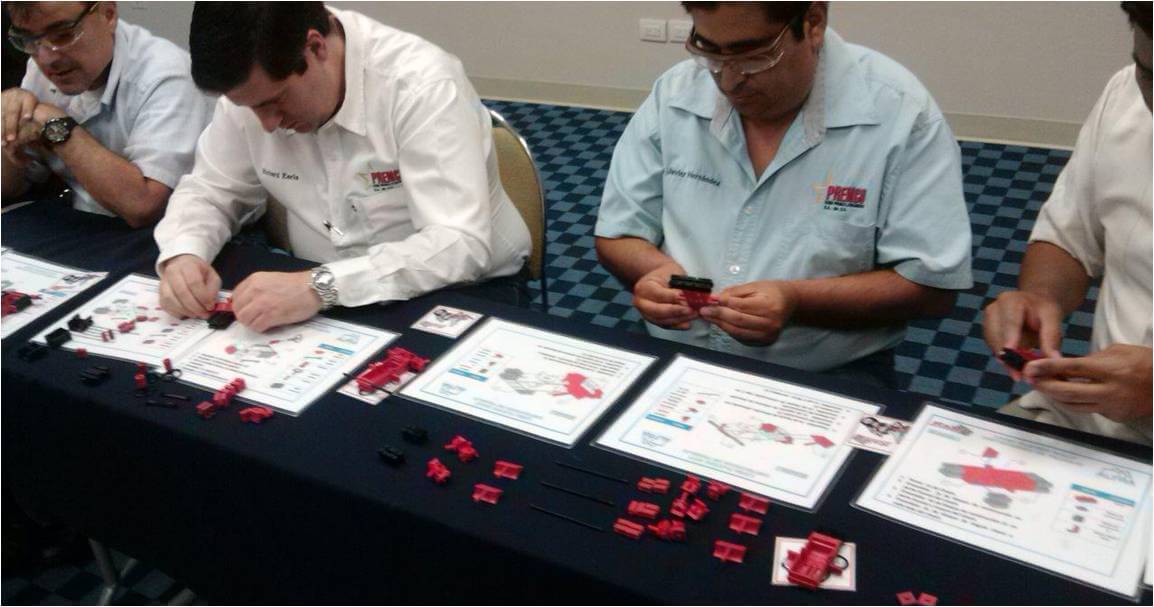
See the case example
Why is so powerful?
Participants get a deep understanding of “why” to apply the Lean principles, identifying and implementing by themselves based on real needs of the process, therefore understanding the real purpose of the systems and tools, this can be learned only by practice.
Participants take part in different roles such: manufacturing workers, material handlers, supervisors, process engineers, general manager, quality engineers, finance, customer service, lean practitioners, among others, giving them an integral view of the operations, not only from his actual function.
Simulation Scopes
From the basic lean concepts session until an integration of all the management systems to reflect improvement on the KPI (performance & financial)
4 hours session is intended to show participants firsthand the comparison between traditional production system and lean production system; this is scope a first step in lean deployment to align all the functions and levels of the company with the lean concepts and benefits, providing the understanding and awareness to enable change in the enterprise.
Recommended for: Put the Management Team in one room and show the benefits of the Lean Implementation in a manufacturing level and specific point in functional relations
8 hours sessions of above can enable a continuous improvement dynamic combining with lean theoretical training and further application of the concepts, participants achieve deep and clear understanding of the principles and how to apply them by creating their own improvements, this is recommended for active lean practitioners in all the areas or the organizations.
From 12 to 24 hours of simulation.
The Group receives a series of progressive challenges making different improvement cycles (PDCA) reaching a high performing & mature operations level, several lean systems and tools are implemented, it is also aligned to the operational excellence model (The Toyota Way) and includes futures for HR & Financial Management, and Strategy Deployment
Recommended for: Lean Managers & Practitioners, and problem solvers in every function that require a deep knowledge of the Lean Philosophy and the integration with an Strategy.
We also have a virtual lean simulation for business process
FLEXIBLE APPROACH
Recommended for all levels:
Senior Managers, Middle levels, Frontline Operators
We adapt the simulation approach & complexity depending on each target audience and learning objective.
The number of participants can vary from 8 to 35, enabling different simulations features according to the amount of participants and time available
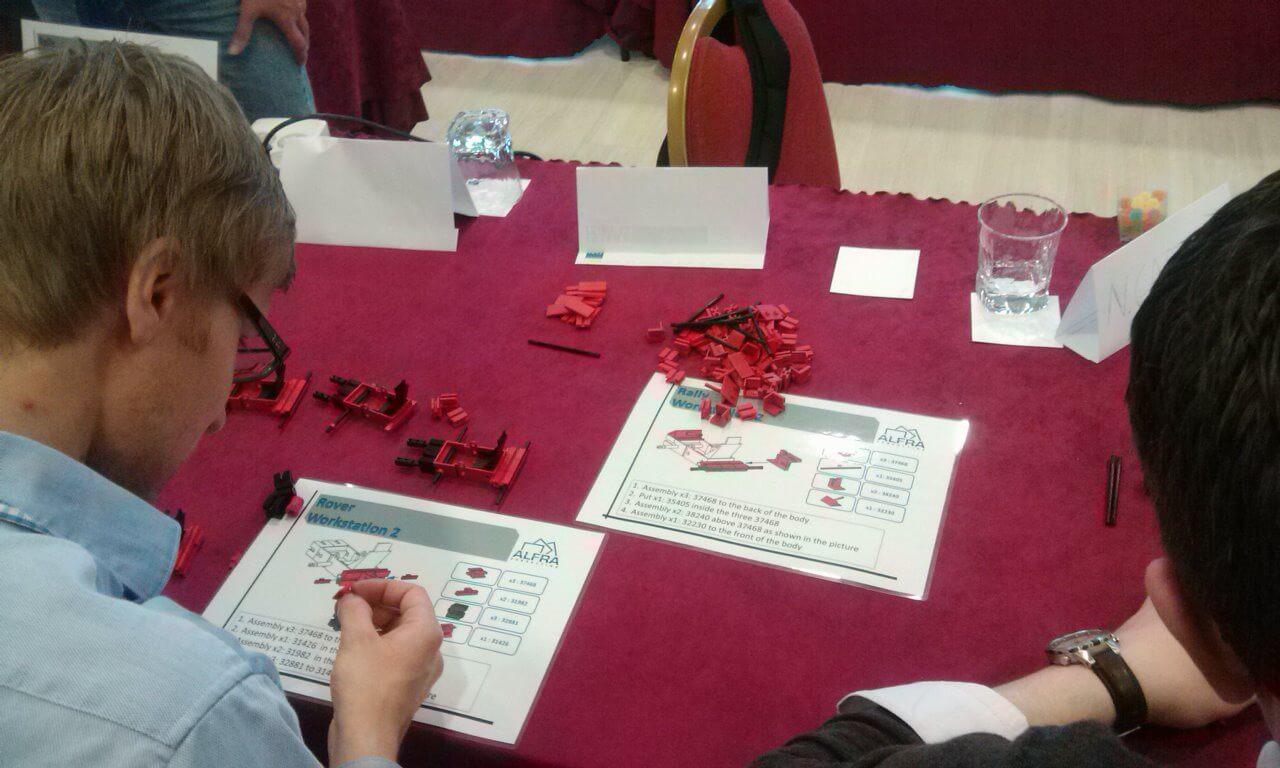
Save your place for the Simulation session
Do you want to take it to your company?
SCHEDULE A CALL WITH OUR CONSULTING TEAM